How to Cross-Train Employees
Cross-training is when you train different employees on a variety of processes so that when you have a call-out or someone’s taking vacation time, you will have others trained to backfill that person. Cross-training creates organizational flexibility and minimizes customer impacts due to a daily staffing shortage.
Cross-Training Matrix: You don’t want to leave your departments cross-training plans up to chance. If you don’t manage to a documented training plan, your customers could suffer the consequences. So instead you want to create a cross-training matrix.
Set goals for each process . – i.e. how many people you want trained for each process. Then you can see where your cross-training plans are meeting target and where you have gaps and you can adjust your training plans accordingly.
CROSS-TRAINING EXAMPLE
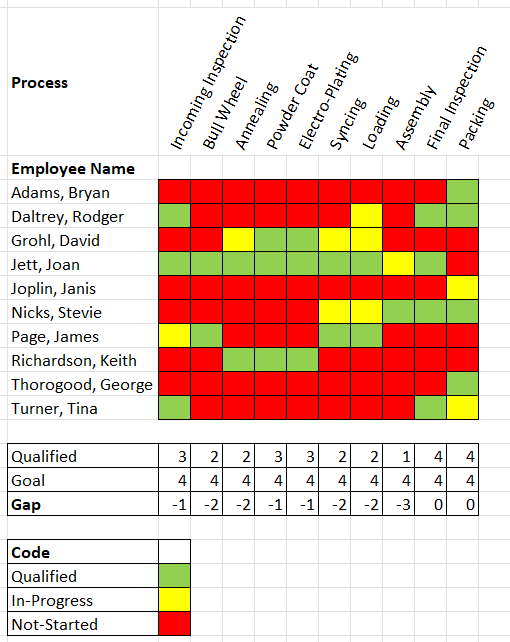
Subject-Matter-Experts (SME's): Next we need to identify and develop a subject-matter-expert for each process that you have in your department. These SME’s as they are called are your go-to people for a given process particular process. They should be the experts. Maybe you have these already on some or all of your processes or maybe you need to identify and develop them. But regardless, you want to specifically name and document the one subject-matter-expert that you have for each process in your department.
Having formal SME’s in your plant will help you in many ways and cross-training is just one way it helps. These SME’s need to be available to you. They need to be the ones developing the process documents and guiding the training, if not actually being the instructor themselves. Ideally these SME’s work in your department. That is the best case scenario!
However, if the SME’s don’t work in your department and they are not accessible to you, then I recommend developing a SME’s in your department. I’ve been successful at this by identifying people in my department and then developing them by having the current on-site SME train my employee and then also sending my SME to some outside training at the OEM’s site.
Once you identify your subject-matter-experts then start working with them to compile all the training material that is currently available. This includes Work Instructions, Quality Procedures and job safety analysis (JSA's).
Next, Work with SME’s to develop a full list of required skills and knowledge. Your SME should be able to easily identify everything that an operator needs to know to effectively operate the process. A good way to do this is to have the SME actually operate the process for a few hours while someone observes and documents all of the actions performed by the SME. Process settings should also be documented.
If you are fortunate enough to have an on-site trainer, that’s awesome! Typically the plant-wide trainer would be the one working with the SME’s to develop the training material, but if you don’t have a trainer, then it’s a good idea that you help develop the material. Starting out with a list of process steps and run-settings, isn’t too difficult or time consuming to tackle.
After you have a good list of everything that is required to run the process, compare that to the documents that you already have. Do the existing work instructions cover everything required? Or are there gaps in the work instructions? SME should create new work instructions if some are missing in the documentation library and they should update the existing documents too if there is missing information. This step is important, but time consuming. If you have missing work instructions, then I wouldn’t let it hold up your training plans. Just have the SME cover the information verbally with the trainees until the Work Instructions are written, approved and released.
Once you have the training requirements and all the work instructions complied then create a training packet. The SME will be the keeper of this training packet and they will provide copies to the trainees. This training packet houses the information that the trainee needs: The packet includes training objectives, training times, the SME’s name This packet also includes a list of required training in a step-by-step format. This packet includes all of the essential documents that the trainee needs such as work instructions, procedure and JSA’s.

Sign-Off Sheet: One of the most important aspects of the training is a sign-off sheet. The sign-off sheet should include the full list of all the required tasks and a place for the trainer to sign-off for each task once the trainee has demonstrated proficiency on that on skills. Once all of the lines are signed-off, then the employee is qualified. It’s important to keep tis training record in the employees file. Audit teams, including ISO, require documentation that training was effective.
Summary: Cross-training is usually focused on providing employees a wider-base of process knowledge and skills. Cross-training lateral development. Some companies do have systems in place that financially reward broader knowledge and skills. So as employees gain lateral skill blocks, they also receive small pay increases too. This is not the norm, however.
Cross-Training is a game-changer! Leadership Development is a results getter! Checkout Tools for the Trenches Leadership Training and get RESULTS!
Stay connected with news and updates!
If you want some weekly T4T wisdom coming straight to your inbox for your reading pleasure - look no further! Join our mailing list to receive the latest blogs and updates.
Don't worry, your information will not be shared.
We hate SPAM. We will never sell your information, for any reason.